Behind the Scenes: A day in the Life at Shocklayer
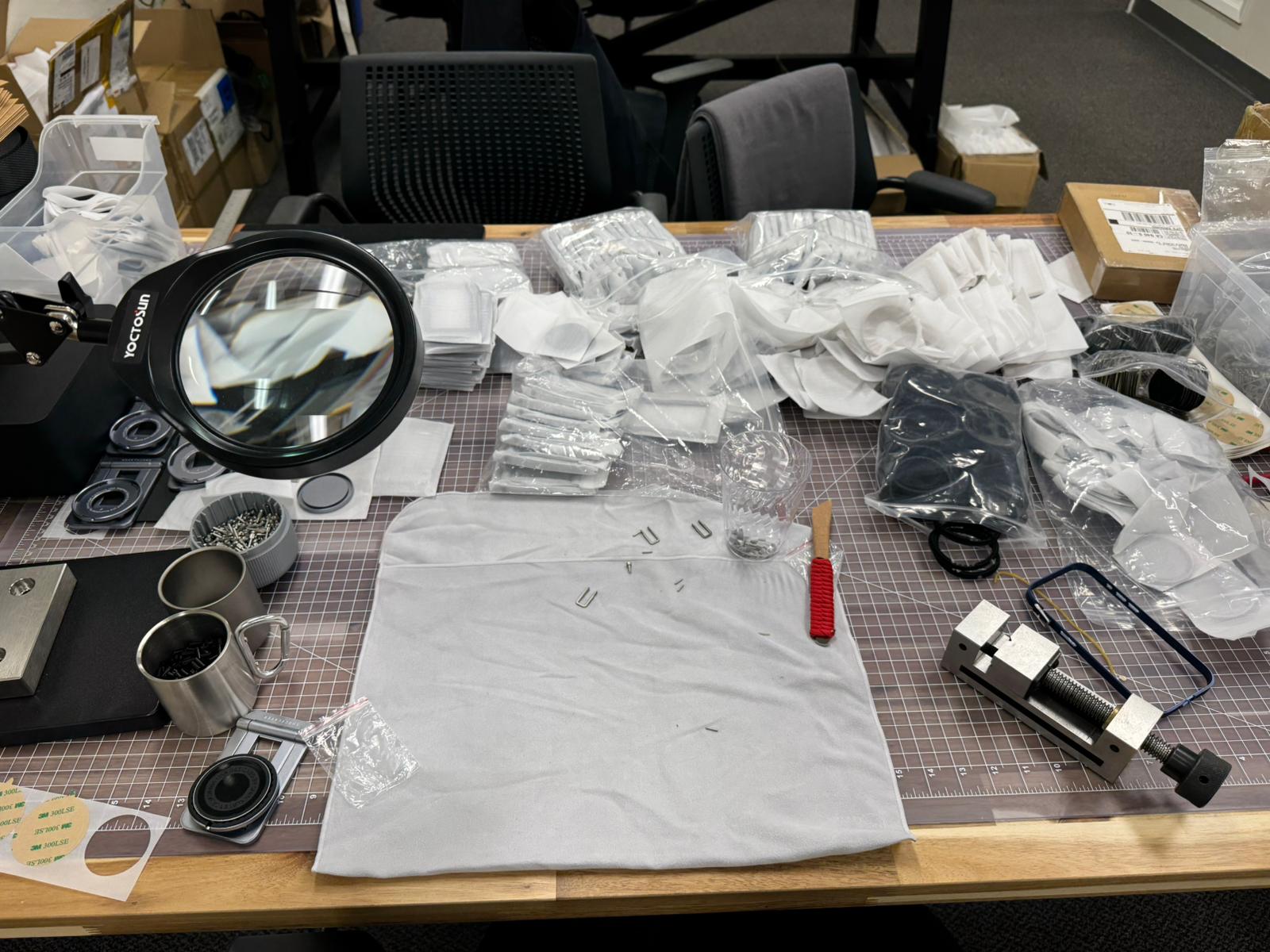
At ShockLayer, what you see on your screen is just the tip of the iceberg. Behind every product is a world of meticulous craftsmanship, innovative design, and rigorous testing. In this special behind-the-scenes look, we’ll take you on a journey through the processes and people that make ShockLayer products stand out in the crowded tech accessory market.
1. Conceptualization and Design: Where Ideas Come to Life
Every great product begins with a spark of inspiration. At ShockLayer, our design process starts with understanding the needs of our customers. Our team of industrial designers and engineers brainstorm and sketch out ideas that blend functionality with style. Whether it’s a phone case, laptop stand, or belt, each concept is carefully crafted to solve a problem or enhance the user experience.
Your Input Matters: We often gather feedback from our customers during this stage, ensuring that the final product reflects the real-world needs of the people who use it.
2. Material Selection: Choosing the Best for Durability and Sustainability
Once the design is finalized, the next step is choosing the materials that will bring it to life. We prioritize materials that are not only durable but also sustainable. Our use of aerospace-grade aluminum, for example, ensures that our products are lightweight yet incredibly strong. Plus, aluminum’s recyclability aligns with our commitment to reducing environmental impact.
Sustainability in Action: Every material we choose is vetted for its environmental footprint, ensuring that we’re creating products that are built to last and built to protect the planet.
3. Prototyping and Testing: Turning Concepts into Reality
With the design and materials ready, we move on to prototyping. This is where our ideas start to take physical form. Prototypes are created and then put through a series of tests that simulate real-world conditions.
Rigorous Testing: From drop tests to stress tests, we push our products to their limits to ensure they meet our high standards for rugged reliability. Our goal is to identify and address any weaknesses before the product goes into full production.
4. Manufacturing Excellence: Precision and Quality at Every Step
Once a prototype passes our stringent tests, it’s time for manufacturing. We partner with top-tier manufacturing facilities that share our commitment to quality. Each product is carefully assembled with precision, ensuring that every detail is perfect.
Quality Control: During manufacturing, our team conducts continuous quality checks to ensure that every batch meets our exacting standards. This includes everything from inspecting material quality to ensuring that every part fits together seamlessly.
5. Real-World Feedback: Testing with the Pros
Before we release any product to the market, we put it in the hands of real-world professionals—photographers, travelers, urban planners, and more. These experts use ShockLayer products in their daily lives, providing us with valuable feedback that helps us refine and perfect our offerings.
Continuous Improvement: This stage is critical for us to make any final adjustments and ensure that our products truly meet the needs of our customers.
6. The Final Product: From Our Hands to Yours
After all the hard work, our products are ready to be released into the world. But our job doesn’t end there. We continue to monitor customer feedback and stand by our products with a lifetime warranty, ensuring that every ShockLayer customer enjoys the best in rugged reliability.
A Shared Journey: When you purchase a ShockLayer product, you’re not just buying an accessory—you’re joining us on a journey of innovation, quality, and sustainability.
Discover ShockLayer today and experience the passion, precision, and care that goes into every product we make.
Leave a comment